Windows and doors
How do I specify windows that comply?
Under the schedule method in H1/AS1 5th edition amendment 1, the minimum construction R-value for vertical windows and doors is R0.46 in climate zones 1–4 and R0.50 in climate zones 5 and 6.
It is possible to reduce the construction R-values of windows and doors below the levels required in the schedule method by instead using the calculation or modelling methods to demonstrate Building Code compliance. The calculation method is explained in H1/AS1 and the modelling method in H1/VM1.
These methods allow the use of windows and doors with lower construction R-values if the construction R-values of other building elements – floor, walls or roof – are increased to compensate.
How do you know that a particular set of windows will comply with the Building Code construction R-values?
The requirements for working out the construction R-value of windows, doors and skylights are given in Appendix E in H1/AS1 and H1/VM1.
Table E.1.1.1 for vertical windows and doors in Appendix E in H1/ AS1 is to be used for housing only. For other building types, use the calculation method in H1/VM1.
The table does not apply to opaque doors or opaque door panels – see the next question.
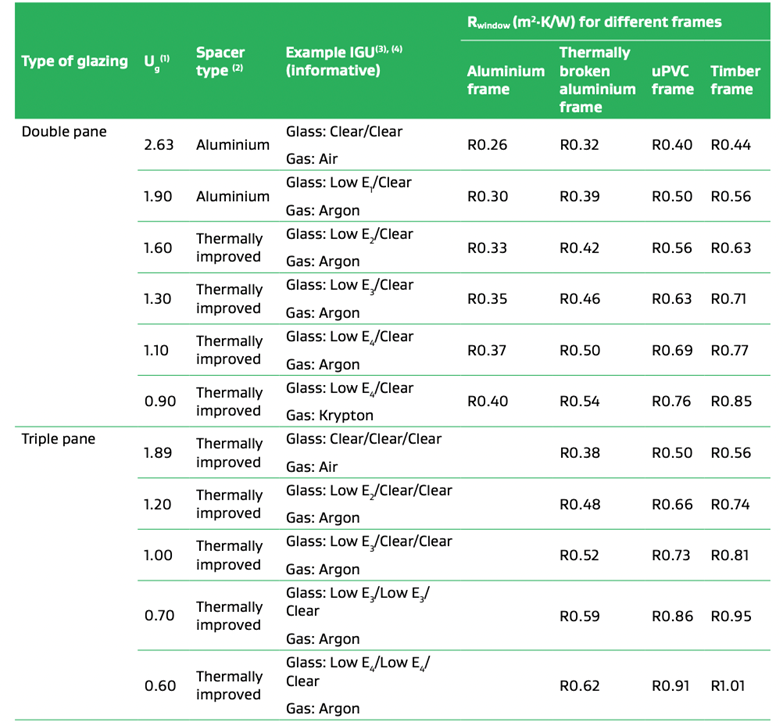
The table for vertical windows cannot be used for skylights. Ask skylight suppliers for details.
How do I find out more about doors, including opaque doors?
Windows and doors are treated together in H1/AS1 and H1/VM1 5th edition amendment 1. The requirements for windows and doors cover opaque doors or doors with opaque panels.
The schedule method
The schedule method in H1/AS1 requires a minimum construction R-value of R0.46 for vertical windows and doors in climate zones 1–4 and R0.50 in climate zones 5 and 6.
One of the restrictions with the schedule method is that you can only use it if the opaque door area is no more than 6 m2 or 6% of the total wall area, whichever is greater. If your opaque door area exceeds this, or you want to be able to install windows and doors with lower thermal performance than the schedule method requires, you must use the calculation or modelling methods.
The calculation and modelling methods
The calculation method in H1/AS1 and the modelling method in H1/VM1 can be used to reduce any of the elemental schedule method figures if insulation in other building elements (unheated floors, walls or roofs) is increased to compensate. The calculation method can only be used on buildings where glazing makes up 40% or less of the total wall area, but the definitions of ‘glazing area’ and ‘wall area’ both exclude opaque doors or door panels.
Clause 2.1.3.6 in H1/AS1 shows where opaque door areas fit into the calculation method heat loss equation for the proposed building.
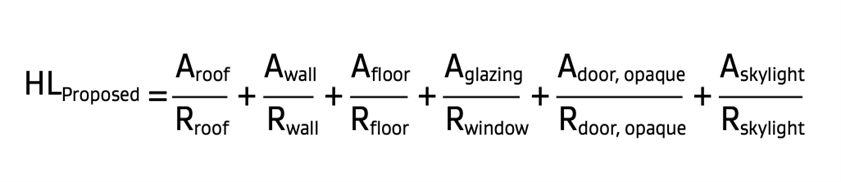
In the equation, HLProposed is the heat loss of the proposed building, Adoor, opaque is the opaque door area in m2 and Rdoor, opaque is the construction R-value of the opaque door area.
In the equation, the opaque door area is the total area of opaque doors and opaque panels of doors in the thermal envelope, including frames and opening tolerances. If there are two separate opaque doors with different levels of thermal performance, you can treat them separately, splitting them into two parts in the equation.
Acceptable methods for determining the construction R-values of opaque doors and opaque door panels are given in NZS 4214: 2006 Methods of determining the total thermal resistance of parts of buildings.
Clause 2.1.3.9 in H1/AS1 states that where the construction R-value of a building element is not known, default construction R-values of 0.18 m2 ·K/W for an opaque building element must be used in the heat loss equation for the proposed building.
For the modelling method, section D2.4 in H1/VM1 states that in the reference building:
a) The opaque door area that is no more than either 6 m2 or 6% of the total wall area (whichever is greater) shall have the same construction R-value as the reference building windows (or higher at the designer’s discretion); and
b) Any remaining opaque door area shall have the same construction R-value as the reference building wall.
A comment in E.1.2.3 of H1/VM1 states that the door construction R-value includes the effects of the frame, any glazing, and any opaque panels.
Secondary insulation in walls and roofs
How do I use secondary insulation layers to increase the R-value?
One construction approach that can lead to a big improvement in the thermal performance of a wall or roof is a secondary insulation layer. How big an improvement? Almost a doubling in wall and roof construction R-value can be achieved in some circumstances. You can find examples in the BRANZ House insulation guide 6th edition.
With walls, the secondary insulation layer commonly takes the form of a cavity constructed with horizontal timber battens spaced to suit the installation of insulation and direct fixed interior linings. Additional bracing may be needed. This could be provided by a rigid underlay on the outside or additional bracing (such as plywood) between the two insulation layers. It is important to ensure that the interior lining is airtight to reduce the risks of moisture transfer.
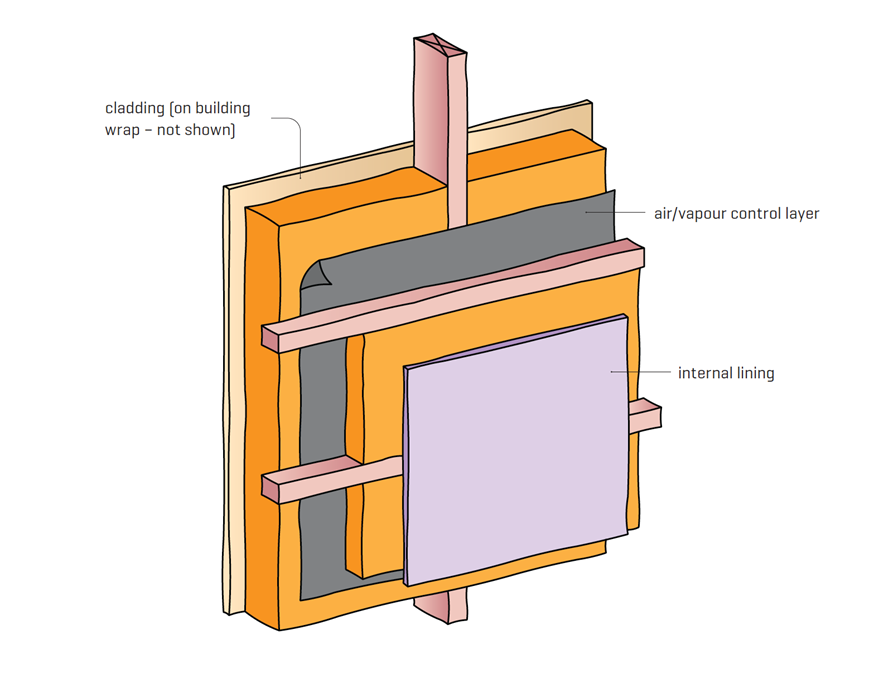
A similar approach can be followed with roofs.

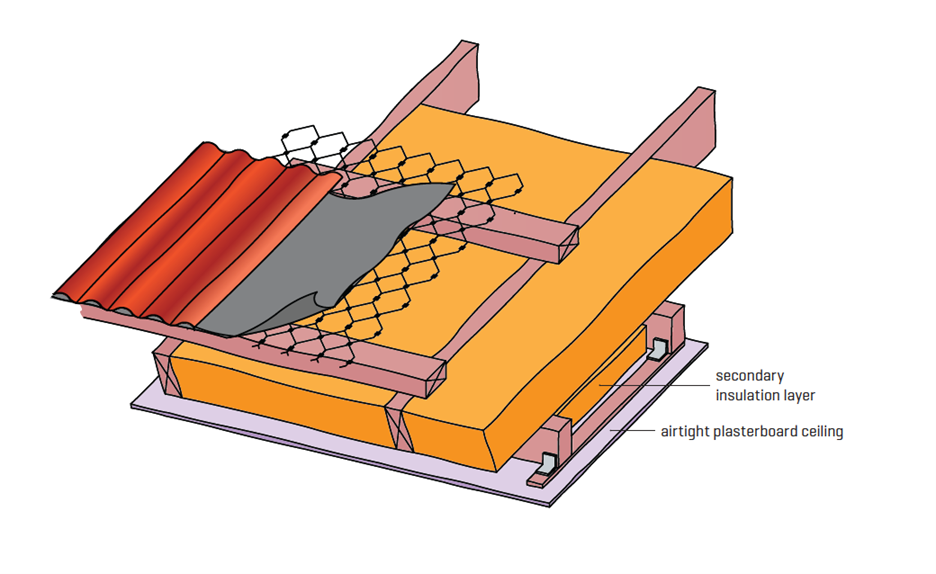
The battens for the secondary insulation layer should be fixed at right angles to the main framing members to reduce thermal bridging. Where strips of blanket insulation are installed, they should also be installed at right angles to the primary insulation.
With roofs as with walls, it is important to ensure that the interior (ceiling) lining is airtight to reduce the risk of problems with moisture transfer from the living spaces.
The use of a secondary insulation layer should be determined early in the design process and discussed with the frame and truss manufacturer at an early stage.
Concrete slabs
How do I deal with concrete slabs with attached unconditioned spaces such as garages?
While a garage commonly sits on its own separate slab, one step down from the finished floor level of the habitable area of the dwelling, there are cases where an attached garage occupies the same slab-on-ground floor as habitable spaces.
H1/AS1 defines unconditioned space as: “Space within the building envelope that is not conditioned space (for example, this may include a garage, conservatory, atrium, attic, subfloor, and so on). However, where a garage, conservatory, or atrium is expected to be heated or cooled these spaces shall be included in the conditioned space.”
H1 does not require unconditioned spaces to be insulated, but Appendix F of H1/AS1 – the appendix that covers the thermal resistance of slab-on-ground floors – makes the comment:
“Since insulation cannot be easily retrofitted to slab-on-ground floors, it is recommended to also insulate the floor of any unconditioned spaces of the building, where these may become conditioned spaces at a later stage during the building life. An example is an attached garage that could potentially be converted into a habitable space in the future.”
Where this is not done, another comment in Appendix F of H1/AS1 applies: “Any parts of a slab-on-ground floor that are not part of the thermal envelope (such as the floor of porches, attached garages or storage areas) should be thermally separated by installing vertical edge insulation in between conditioned and unconditioned parts of the floor.”
Thermally separated edge insulation within slabs is not currently common practice and may require specific design by an Engineer to consider any impact on the foundation design, reinforcing and load bearing capacity of the slab at this junction. Minimum slab thicknesses should not be compromised.
Note: NZS3604:2011 clause 7.5.10 states that “ Thermal insulating material may be used provided that there is no reduction of any dimension given by this standard.
While an attached garage can be considered as an unconditioned space and thermal insulation could be installed between the two slabs, Engineers (and designers) will need to consider what happens at wall / roof level between the two structures if they are separated and how they might be tied together. This will likely have design, build and cost implications and the owner / builder may prefer to install the insulation under the unconditioned space to save costs and ‘future proof’ as mentioned above.
How do I comply with the rules around slab-on-ground with embedded heating?
The H1/AS1 schedule method has minimum construction R-values for heated ceilings, walls or floors, set out in Table 2.1.2.2.A:
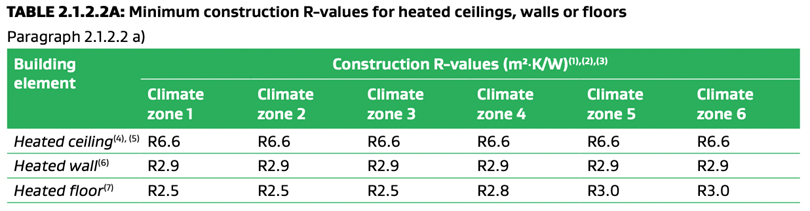
The calculation method cannot be used to reduce the performance of slab floors with embedded heating systems – the minimum construction R-values in the schedule method apply.
Appendix F in the new H1/AS1 and H1/VM1 gives an acceptable method for determining the construction R-values of slab-on-ground floors, with extensive tables in H1/AS1 showing construction R-values for selected slab-on-ground floor scenarios. The generic types of slabs include raft foundation slabs for the first time.
Updated: 04 December 2023